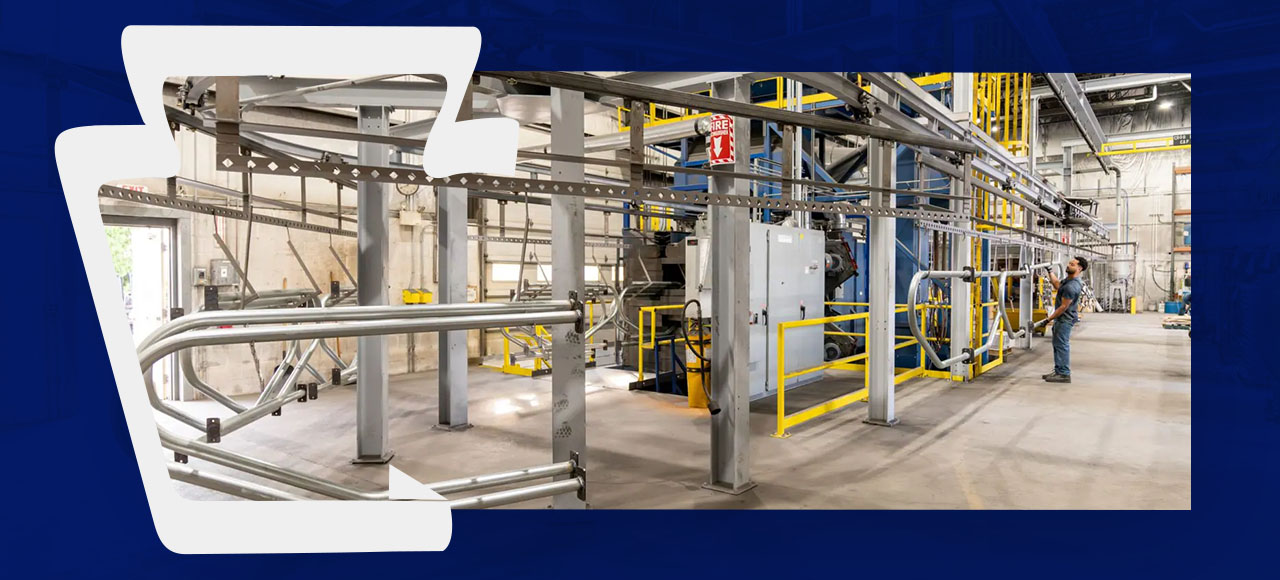
When you’re preparing metal parts for powder coating, the finish is only as good as the surface underneath. That’s where industrial sandblasting plays a critical role. If you’re a manufacturer or product fabricator aiming for durability, corrosion resistance and a flawless finish, understanding what sandblasting is and why it’s essential before coating is crucial for your business.
This article highlights how sandblasting works, why it’s a vital step before applying powder coating and how it directly affects longevity and the overall quality of your finished product.
What Is Sandblasting?
Sandblasting is a surface preparation process in which abrasive materials, commonly referred to as “media,” are blasted at high speed onto a surface to clean it, roughen it or remove contaminants. In industrial settings, this technique is commonly used to prepare metal surfaces prior to powder coating, ensuring optimal adhesion and finish.
In industrial sandblasting, compressed air propels abrasive particles, such as steel grit, aluminum oxide or crushed glass, through a nozzle, creating enough force to strip away imperfections and create a consistent texture across the material. This texture is what helps the powder coating bond effectively.
Whether you work with steel, aluminum or other metallic materials, sandblasting provides a clean, etched surface that’s ready for the next phase in the finishing process.
How Sandblasting Works
Understanding how sandblasting works helps you see why it’s a critical part of the metal finishing process. Whether you’re preparing parts for industrial powder coating or removing years of corrosion, here’s the general overview of the process:
- Surface inspection: Before blasting begins, the surface is examined to determine the type of contamination and the best abrasive media for the job.
- Media selection: Depending on the material and the desired finish, technicians choose from a variety of abrasive options, such as aluminum oxide, steel grit or glass beads.
- Abrasive blasting: High-pressure air pushes the abrasive material through a nozzle, directing it toward the surface at high velocity. This action removes old coatings, rust, oil or mill scale, creating a uniform surface.
- Surface cleaning: After blasting, the surface is cleaned to remove residual dust or debris. What remains is a bare, properly textured surface ideal for coating.
- Inspection and quality check: The surface is checked to ensure it meets specifications for cleanliness and texture. Only then is it considered ready for powder coating.
While sandblasting seems like a cleaning process, it’s specifically designed to create the right conditions for long-lasting finishes. Sandblasting’s consistency and control make it indispensable to the powder coating process.
Why Sandblasting Is Important Before Powder Coating Metal
If you’re preparing metal products for powder coating, sandblasting is a key step that’s necessary for a high-quality and professional finish. Here’s why it matters:
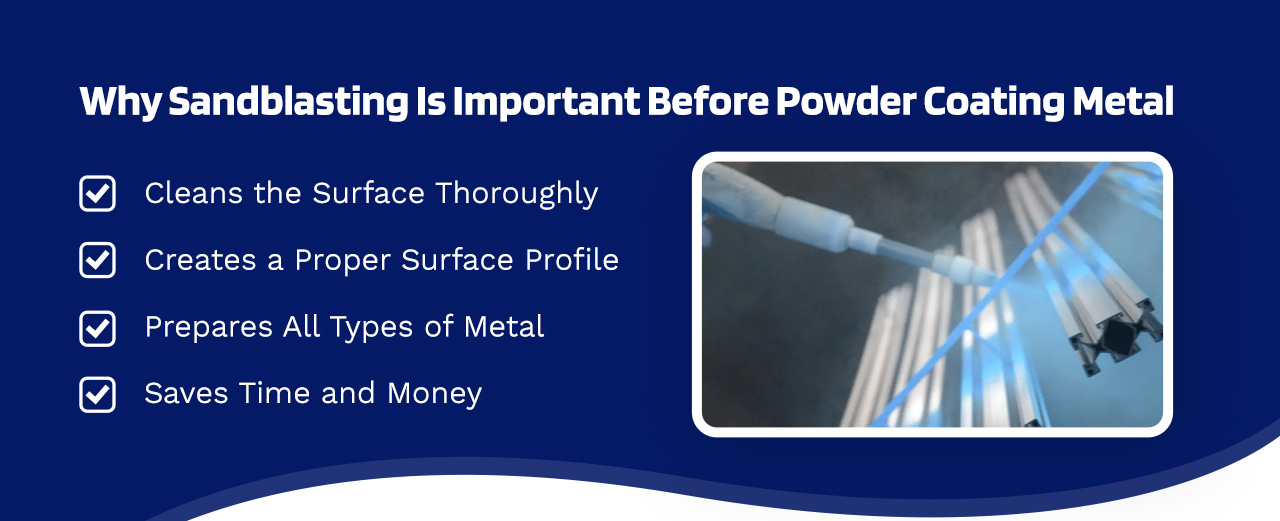
1. Cleans the Surface Thoroughly
Metal straight from fabrication often contains contaminants such as oil, dirt or rust. These materials interfere with powder coating adhesion, leading to uneven coverage, chipping or peeling. Sandblasting removes these surface inconsistencies.
2. Creates a Proper Surface Profile
Powder coating doesn’t bond well to smooth, slick metal. Sandblasting etches microscopic depressions, also known as anchor patterns, into the surface. The resulting rough surface promotes coat adhesion, prevents peeling and creates a uniform finish.
3. Prepares All Types of Metal
Whether your product line involves steel, aluminum or other metals, you can still benefit from sandblasting. The process works with all metals, including softer ones like brass and copper. With commercial sandblasting services, specialists customize hardness levels to match different surface needs.
4. Saves Time and Money
Sandblasting is fast and effective in removing old paint, rust and surface contaminants. The outcome is an ideal surface texture that promotes adherence, ensuring a strong bond between the powder coating and the metal. Beginning with sandblasting minimizes the risk of the coating peeling and flaking, which would mean costly reapplications and downtime.
Benefits of Sandblasting for Powder Coating Adhesion
For your powder coating to last, proper adhesion is crucial, and sandblasting is the most effective way to achieve it. Here’s how sandblasting directly improves powder coating performance:
- Superior bonding surface: Sandblasting creates a textured surface that allows powder particles to anchor themselves firmly. This strong mechanical bond prevents flaking, chipping and bubbling after the material has cured.
- Even coverage: With a clean, prepped surface, powder is distributed more evenly across the metal. That means a consistently professional finish on every surface you work on.
- Fewer failures and returns: Poor adhesion leads to premature coating failure. Sandblasting before applying powder coating reduces product defects, customer complaints and costly do-overs.
- Reliability in harsh conditions: A key impact of sandblasting on powder coating durability is how well protected the surface becomes after the treatment. A powder coat that sticks properly protects your product from moisture, salt, UV rays and chemicals. Sandblasting enhances this resistance by creating conditions that promote adhesion.
Investing in sandblasting solutions pays off by ensuring your powder coating looks good and holds up under real-world use.
Impact of Sandblasting on Powder Coating Durability
When it comes to powder coating, long-term durability is desirable, especially for products exposed to weather, abrasion or heavy industrial use. Here are some of the impacts of sandblasting on powder coating durability:
- Resistance to wear and tear: A properly sandblasted surface ensures the powder coat doesn’t peel, blister or wear down prematurely. That means your coated products maintain their appearance and performance much longer.
- Protection against corrosion: Rust and corrosion often start beneath the coated surface. Sandblasting strips away oxidation, old coatings and contaminants that could cause corrosion later. This clean base helps powder coatings form a tough, impenetrable barrier against moisture and environmental exposure.
- Increased lifespan of metal products: When you combine a thoroughly prepped surface with a high-performance powder coat, you get a finish that stands the test of time. This translates into fewer repairs and replacements.
- Good return on investment: A longer-lasting product delivers a better return on investment. Sandblasting before powder coating ensures you get the most out of your materials, labor and coating process.
Sandblasting directly improves the durability of powder-coated metal, making it a wise choice for any business focused on long-term quality.
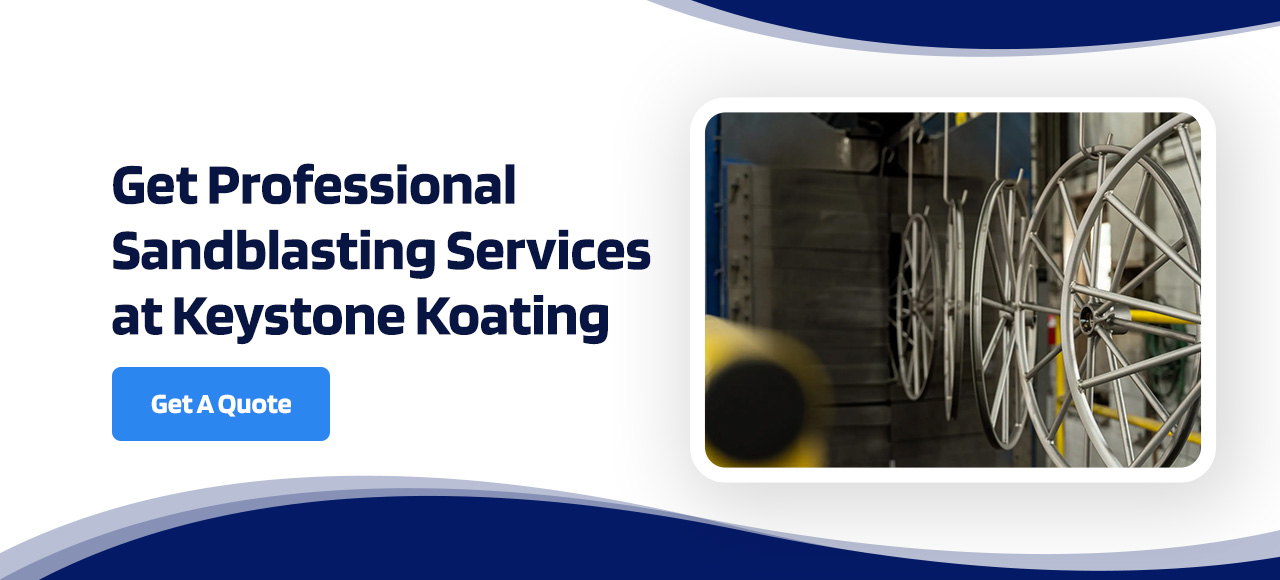
Get Professional Sandblasting Services at Keystone Koating
Sandblasting is a critical process that prepares metal for flawless adhesion, increases the longevity of coatings, and protects products from premature wear and corrosion. Ultimately, it’s the difference between an average finish and a professional one.
At Keystone Koating, we provide industrial sandblasting and high-quality powder coating services that meet the highest standards. Whether you manufacture heavy-duty equipment or intricate metal parts, we help you get the finish that protects your product and your reputation.
Contact us or request a quote to learn more about our sandblasting solutions and how they can give your next project the edge it needs.