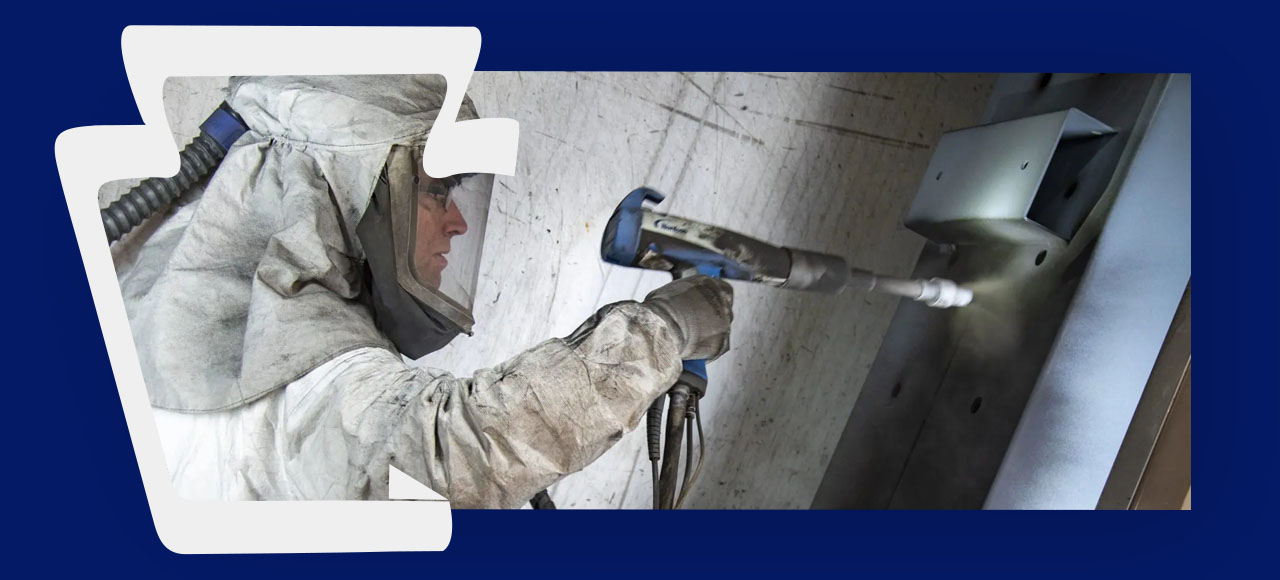
In architecture, every detail of a structure reflects your brand, your standards and how much you value quality. For this reason, high-quality finishes are necessary both for aesthetics and optimal performance. While the application of powder coating in architecture offers exceptional surface-level appeal, it also plays a critical role in protecting structures from corrosion, UV damage and wear over time.
Whether you’re overseeing large-scale production or sourcing materials, choosing the right surface finish will significantly affect client satisfaction.
What Is Architectural Powder Coating?
Architectural powder coatings are high-quality finishes designed for metal components used in construction and building projects. Unlike traditional liquid paints, these coatings are applied as a dry, electrostatically charged powder that bonds to the surface and is cured under heat. The result is a uniform, durable finish that resists corrosion, fading, chipping, wear and harsh environmental conditions.
While protection drives the use of powder coatings in architecture, they also offer a wide range of colors, gloss levels and textures to cater to both aesthetic and functional needs. Whether you’re managing a commercial project or producing building materials, architectural coating solutions can deliver consistent, high-quality results.
How Is Powder Coating Used in Architecture?
Architectural powder coatings are often applied to exterior building features that are exposed to intense UV radiation, moisture and pollutants. These include:
- Façade panels: Powder-coated panels offer weather resistance, color retention and low maintenance for exterior façade panels. They help structures withstand UV exposure, moisture and pollutants without degrading in appearance or performance over time.
- Doors and windows: Powder coating provides a smooth, chip-resistant finish on aluminum and steel frames, enhancing the durability of these high-touch areas.
- Railings, fencing and balconies: Architectural elements exposed to the elements require finishes that can withstand pressure. Powder coatings resist corrosion and fading, extending the life of structures such as railings and guardrails.
- Architectural metalwork: Thanks to an efficient powder application process, powder coatings make it easy to achieve consistent color and smooth coverage on complex shapes, such as louvers, soffits and custom decorative pieces.
- Curtain wall systems: These aluminum-framed walls benefit from high-performance coatings that resist chalking, cracking or peeling, keeping buildings looking clean for years.
Interior Powder Coating Applications
Inside buildings, powder coating is used for a range of elements that need both form and function. Some common interior uses include:
- Partition systems: Powder-coated partitions maintain a modern look while offering excellent resistance to scratches, scuffs and corrosion.
- Ceiling grids: These systems benefit from a uniform, long-lasting finish that holds up well in environments with fluctuating humidity.
- Metal furniture: Powder coating adds both resilience and visual appeal to desks, chairs and shelving, making it a wise choice for busy offices and institutions.
- Ventilation components: A durable finish protects vents and diffusers from rust and grime buildup, helping maintain cleaner air and a professional appearance.
- Stairways: Handrails and supports receive a tough coating that withstands frequent use, all while complementing the overall design of interior spaces.
Why Choose Powder Coatings for Architecture?
When you’re responsible for delivering high-quality architectural components, performance and longevity matter, and powder coatings for architecture are engineered to deliver both. Here’s why they stand out as a preferred solution across the construction and manufacturing industries:
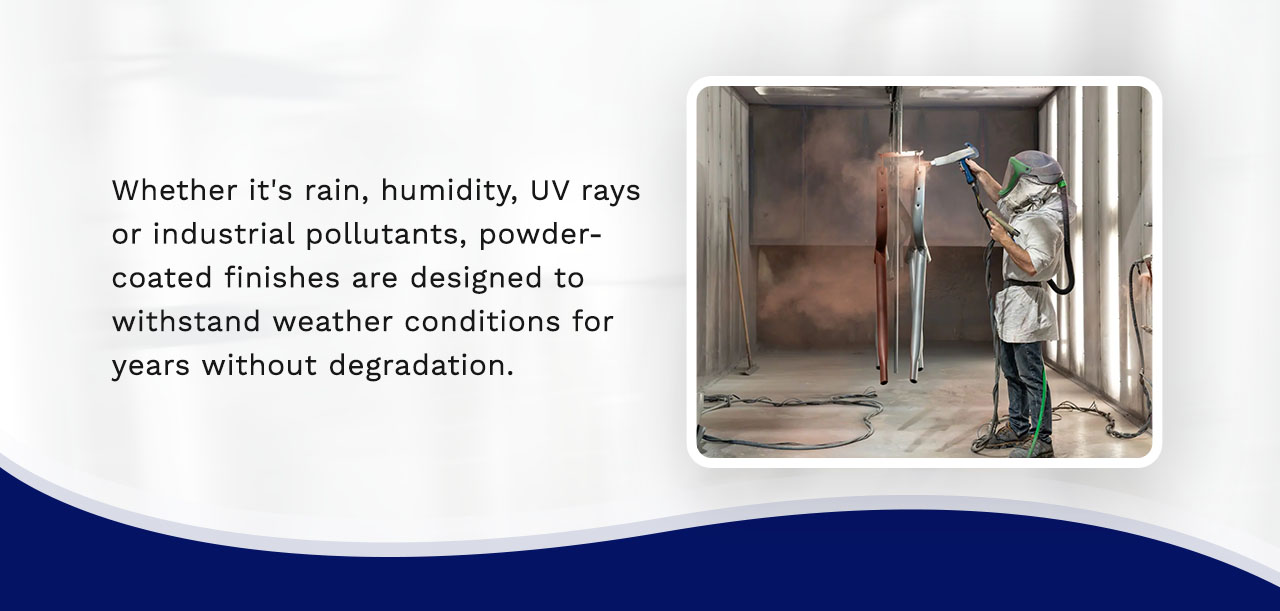
1. Exceptional Durability
Architectural powder coatings form a strong, bonded layer that resists impact, abrasion, corrosion and weather exposure. This is especially important for exterior metal parts that need to endure decades of harsh environmental conditions and high traffic. Whether it’s rain, humidity, UV rays or industrial pollutants, powder-coated finishes are designed to withstand weather conditions for years without degradation.
2. Superior Corrosion Resistance
With the proper surface preparation, including blasting and an eight-stage pretreatment system, powder coating creates excellent adhesion that guards against corrosion. It’s ideal for metal components exposed to outdoor conditions, moisture and chemicals. As such, powder coating provides reliable corrosion resistance to building materials such as window frames, railings and panels.
3. Environmental Sustainability
Architectural coating solutions help reduce your project’s environmental impact. Powder coatings contain no volatile organic compounds or solvents, making them a safer, cleaner alternative to liquid paint. They also allow for overspray recovery, which minimizes waste and improves efficiency.
In addition, the long lifespan of powder-coated surfaces reduces the need for regular touch-ups and replacements, further contributing to sustainable practices.
4. Design Flexibility
Powder coatings offer a broad range of colors, from classic shades to customized options designed to complement your design preference. They also come in diverse finishes that offer creative flexibility, such as high-gloss, matte, textured and faux-style finishes. The diverse options provide ease and flexibility, whether you’re designing for a minimalist modern build or a bold architectural statement.
When it comes to consistency, the electrostatic application process offers a smooth and uniform finish that lacks the challenges of liquid paint, such as runs and sags.
Meeting Architectural Standards and Certifications
Selecting powder coating for an architectural project goes beyond a robust finish. You’re choosing performance that meets strict regulatory and industry standards. Architectural powder coatings are engineered to meet demanding specifications for durability, safety and environmental compliance, including:
AAMA Standards
Architectural powder coatings are formulated to meet standards from the American Architectural Manufacturers Association (AAMA). Some of their standards include:
- AAMA 2603: Standard specification for durability. Best for interior applications or for areas that incur less critical weathering.
- AAMA 2604: Super durable specification designed for exterior architectural applications. Coatings in this class offer resistance to chalking and erosion and have good color retention.
- AAMA 2605: Hyper-durable specification that represents the highest performance standard. Recommended for products with superior qualities that can withstand harsh environments.
QUALICOAT
QUALICOAT is a globally recognized and industry-leading quality label organization. It focuses on quality assurance for painting and coatings on aluminum and its alloys for architectural applications. The organization has established specifications that ensure the superior quality of coated products in architectural applications. QUALICOAT certifications cover strict testing for adhesion, gloss retention, impact resistance, color consistency and more.
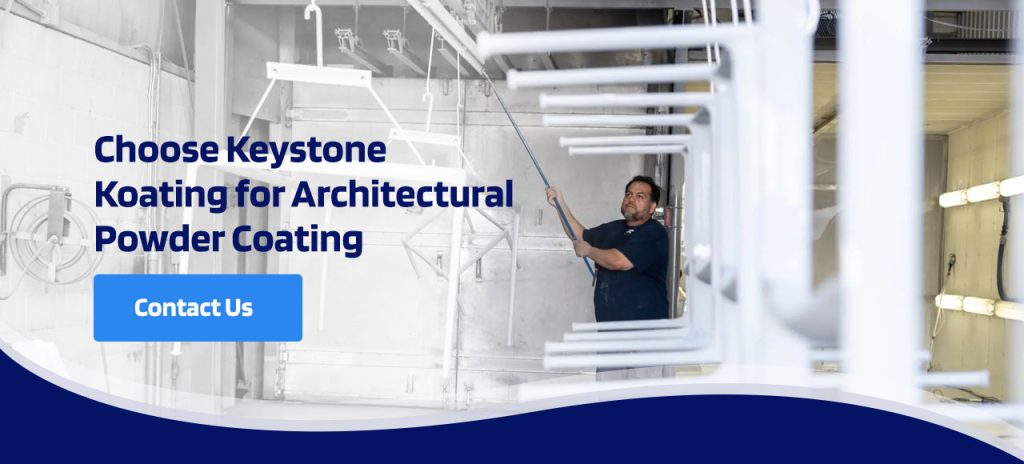
Choose Keystone Koating for Architectural Powder Coating
If you’re sourcing a durable, efficient and high-performance finish for your architectural components, powder coating delivers proven value. At Keystone Koating, we specialize in powder coatings for architectural applications designed for real-world environments.
From blasting and pretreatment to masking, coating and curing, we offer a complete line of architectural coating solutions tailored to your project specifications. Whether you’re producing aluminum panels, railings, louvers or frames, our high-volume capabilities and extensive experience ensure you receive consistent quality on schedule.
Learn more about our full-service capabilities. Contact us today, and let’s discuss your project!